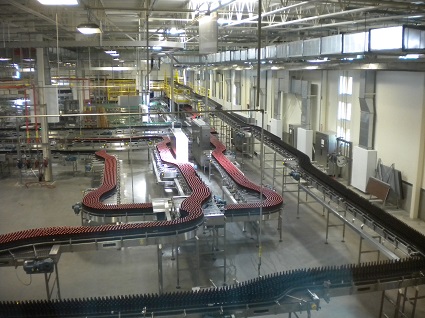
We often hear from engineers or plant managers when they are in a state of emergency. Stress-filled voices reveal that the caller is brushing sparks off his shirt while people in the background shout about how much each minute is costing. We may not hear the line workers standing around helplessly, but we know they’re there.
The call is smart. When your Rexroth electric industrial motion control systems are in need of service and support, we can get you back up and running fast. We’re Rexroth specialists, and we have the nation’s largest inventory of remanufactured Rexroth and Indramat components.
But the sudden emergency shutdown is not the best way to start or even to end a day. A planned shutdown for maintenance is a better option.
Will you need a shutdown?
Do you have a legacy Rexroth servo motor running your machinery? These maintenance-free motors have bearings that are lubricated and intended to last for the life of the motor. That life of motor was estimated at 10 years.
Your motor is probably older than 10. We see motors that have been running for 30 years with no problems. But that doesn’t mean that they will run for another 30 years with no problems. A Rexroth or Indramat servo that has been running for more than a decade is a good candidate for reman.
Factory reman involves opening that sealed motor, cleaning everything, and replacing all the wearing parts, including bearings, before closing and sealing the motor again. The motor will be relaquered and returned to you with a new warranty. It will be like new. In some cases, it will be better than new because technology marches on. If the wearing parts in your component have been upgraded and developed since you first bought it, you’ll have the upgraded and developed parts in your remanufactured component.
Clearly, any component nearing the end of its lifespan can benefit from factory reman.
Plan your shutdown in advance
If you run your facility on multiple shifts, you will be better off choosing the most convenient time for a shutdown. This way, you can identify all the components that will need to be removed and repaired. You can divert workers to other tasks. And you can work out a step-by-step plan.
Identify the tasks that need to be done, recognize any jobs that must be outsourced, and assign every task. Having a manager who can step up to clear obstacles during the shutdown will make a big difference in the smoothness of the process. Machine operators will need deadlines for making sure that the machinery is clean, empty, and safe to work with. A countdown or checklist of essential tasks with deadlines can help.
Rexroth drive and control components are modular, and are not designed to be repaired on the machine. They should be removed and sent to us for repair, reman, or replacement. If time is critical, we can facilitate this with charter planes. If you plan to ship the components, make sure you have included shipping time in your timeline.
Be sure you have all the documentation you need for start-up procedures once the repair or replacement is completed. Request manuals for any machinery for which you don’t have a manual on hand.
We can assist with many parts of the process. Call 479-422-0390 for assistance.