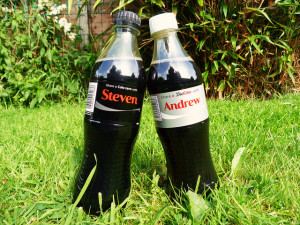
Last year, Coca-Cola did something fun—they removed the iconic label they put on every bottle and instead printed the 250 most popular names in various countries on bottles. Using servo and digital print technology, Coke was able to execute the campaign. The idea was the spark behind a marketing campaign to reconnect Coke with individuals and build relationships between customers who want to share a Coke with their friend. The technology behind the innovative campaign, however, is what really drove it forward and servos played a part.
The project was unique because of the way Coke forced vendors to reveal their secrets of how they’re able to print as well as they do to their competitors—ultimately they all bent over backwards for Coke. It is Coke, after all. Although this technology used HP Indigo digital printers to add the names, the digital printers just added the names whereas the other printing was left up to conventional printers.
In the mix, there had to be some Rexroth printers in the conventional printers who helped Coke in this campaign. Rexroth servos are commonly used in printing press technology because they’re highly reliable and produce high quality prints—which is exactly what Coke wanted for its special campaign. The flexibility of Rexroth servo printers probably played a role in Coke’s campaign.
If your want your company to be able to work with your customers to do things that are completely out of the ordinary, you need to stick with technology that is flexible and be always at the ready. Coke selected five conventional printers out of their huge network of printers—which means they picked the best of the best. If your printing presses aren’t always delivering the highest quality possible on time, choosey customers like Coke won’t choose you for a big project. When you miss out on opportunities like customized Coke labels, you’re missing out on big bragging rights that could bring in even more business to your company.
We can help you stay on track and deliver the best products for every order.