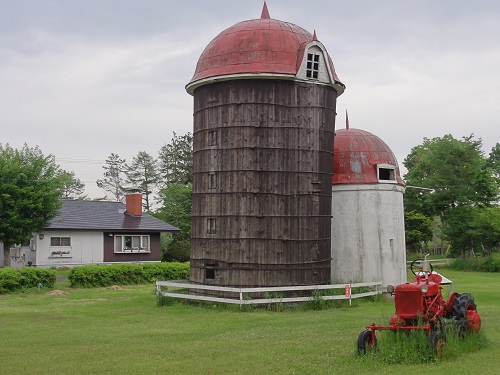
Information silos — those private collections of data that live on desktops, in file drawers, and even in the heads of individual people — can be a real speed bump in the way of progress. When it comes to manufacturing, silos are sometimes built intentionally for reasons that seem good at the time.
Let’s not bother them with these things.
When the marketing department thinks of designers as people who color in the packages, they may not think it matters that the designers understand the overall goal of the new packaging and how it fits into the marketing campaign.
Then some other department provides the engineers with a packaging design made by someone who doesn’t understand its role in the marketing campaign, and they fail to explain the marketing campaign’s goal, possibly because they don’t know what it is.
Later, the marketing department justifies the poor performance of the new package by saying that neither the designers nor the engineers really did what the marketing department envisioned.
Taking a little time up front to make sure that everyone understands the goal can save a lot of time and money down the line. Both the designers and the engineers might have valuable input about how to reach the goal in the most cost-effective and sustainable way, but only if they are involved in the discussion.
They won’t understand it.
A doesn’t think B will understand the data from the focus groups, so that data gets distilled into an order for a certain kind of toy. B doesn’t think that A really gets the sustainability issues involved in toymaking, so the order gets changed and passed on to C. C is sure that B doesn’t realize the structural problems with that order, so the order gets changed a little bit more and goes on to D. D sees a way to improve the workflow, and doesn’t even consider discussing this obvious improvement with A, B, or C.
A might not be conscious of sustainability, structural issues, or workflow, but A is probably going to notice that the product has changed as much in the process of communication as the sentence in a kids’ game of Whispers.
Ideally, all the information along the line will be identified and shared in a clear and understandable way in the early discussions of the product. Then it can all be taken into account before anyone starts sending out orders.
What do they know?
A famous case in a hospital involved intense scrutiny of a particular section of the hospital where infections were more common than in other areas. Administration and top medical professionals spent weeks trying to solve the problem, until at last they asked a nurse, who informed them that the water faucet in that area’s bathroom was broken and had been for months, so it was hard to keep the standard of cleanliness as high as it should have been.
Who might really know the nitty gritty details in your plant? Has anyone asked them?
Machine to machine communication might be key to Industry 4.0, but human communication is always important.