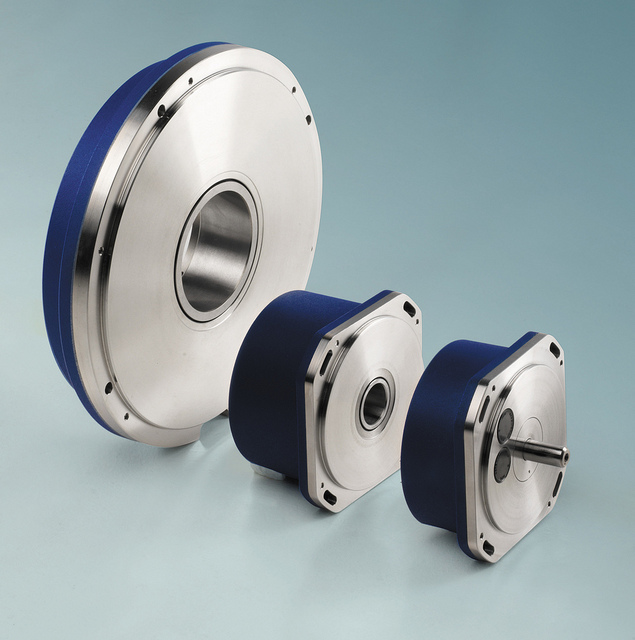
Incremental encoders in Rexroth or Indramat equipment come in a variety of shapes and sizes but they all share one trait: a piece of glass is where the encoding, or directions for the machine, are written. The benefits of these pieces of glass are that highly accurate encoding can be applied and they won’t wear out as quickly as if it they used something like metal or plastic. Glass, when cared for properly, can really stand the test of time.
But glass, despite the benefits of strength and the ability to be encoded easily and accurately, can also break easily if treated improperly. Incremental encoders are not tough when they’re slammed around and can simply bust into a million pieces. Broken incremental encoders means down time for you, delayed orders, and unhappy customers.
Make sure you have the right equipment
How can you avoid incremental encoder disasters in your Rexroth equipment? By making sure your equipment is suited to the job.
This is true across the board. The right size of component for the application always is your best bet. Don’t get the idea that finding something pretty similar on eBay is good enough.
Some equipment is more suited to rough and tumble jobs than others. If you find that you’re breaking incremental encoders often, we can help you get to the root of the problem. It might mean changing equipment to something more robust that can take the brunt of the work. It could even be that someone isn’t treating the equipment correctly.
When you’re transporting your equipment from one location or position to another, be sure to take care not to handle it too roughly, especially if it has an incremental encoder. It’s rare that these cabinets need to be moved but if you’re moving from one location to another or are installing new equipment and replacing old servomotors, make sure to handle them with care—even if they seem tough, there are small and delicate parts inside.