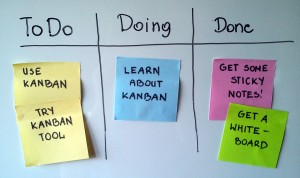
Lean manufacturing is focused on reducing waste. The standard approach looks at seven kinds of waste:
1. Overproduction
Quite simply, overproduction refers to making more product than is needed. Raw materials are tied up in products that may not be sold, space is used to store extra product, and of course energy and resources are used to produce goods that might not be needed.
2. Waiting
Human energy, at the very least, is wasted when there’s a wait between production steps. Waiting for a part to be delivered from one department to another can mean people are idle or that a manager’s time must be spent identifying other work and diverting workers to new assignments. Bringing operators back to the work space and refocusing on the next task introduces further inefficiency.
3. Defects and errors
Defects and errors may require pieces to be melted down or discarded. Identifying and correcting errors takes time and may require stopping and starting machinery.
4. Excess motion and movement
When operators need to step from one place to another or to reach and bend, that’s movement that doesn’t add value. If a machine has to move farther than necessary from its start point to the point at which value-adding work begins, that’s excess motion. Often this is the result of poorly-designed work spaces. The most obvious consequence is lost time, but excessive wear and tear on machinery and the potential for human injury may also be involved.
5. Excess inventory
All companies keep some safety inventory on hand for rush orders and sudden needs.Too much inventory can tie up capital and require time and space for its storage, care, and transport. Skillful forecasting can help.
6. Inefficient processes
Something as small as changing a piece from one hand to the other during work can add up to significant waste over time. Bad habits and poorly set up workspaces or systems can be the culprits here.
7. Excess transportation
Whether it’s shipping cheaper parts from one country to another or moving products from one room to another, any transport that doesn’t add value to the product is waste.
Soon, the lean approach becomes more than a habit — it’s a way of looking at the world.