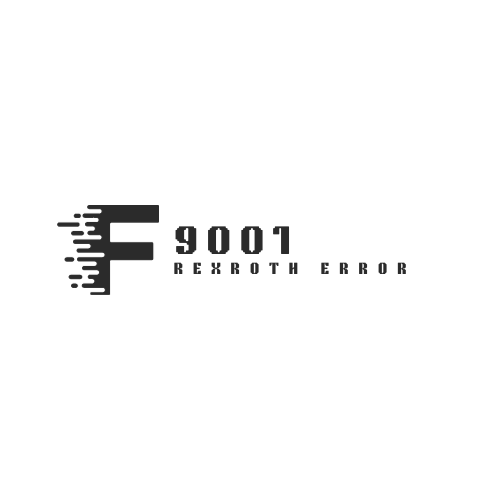
The whirring of machinery suddenly grinds to a halt, replaced by a stark error message flashing on the console: Rexroth F9001. For any operator relying on the unwavering power of Rexroth drives, this code can trigger a surge of adrenaline and frustration. What exactly does it mean, and how do you navigate this technical impasse? Buckle up, because we’re diving deep into the murky waters of F9001.
A Glimpse into the Forbidden Zone
At its core, F9001 signifies a malfunction within the drive’s internal software functions. Imagine the intricate dance of calculations, commands, and processes orchestrating the smooth operation of the motor. F9001 indicates a stumble in this choreography, a critical misstep that throws the entire sequence into disarray.
Causes: A Spectrum of Possibilities
While the error itself paints a bleak picture, identifying the root cause requires detective work. Several culprits could be at play:
- Software Glitches: Bugs and errors lurking within the code can trip up the system. Think of it as a typo in a recipe causing the whole cake to collapse.
- Communication Misfires: Data exchange between various drive components might get garbled or interrupted,leading to confusion and malfunction. Picture crossed wires sending the wrong signals to the orchestra conductor.
- Hardware Faults: Although less common, hardware degradation within the drive’s electronics can disrupt internal processes. Think of a worn-out instrument throwing off the entire musical harmony.
Taming the Beast: Diagnostic Strategies
Confronting F9001 demands a two-pronged approach: immediate action and thorough investigation.
- Restart and Reset: The first line of defense is a simple power cycle. Sometimes, a fresh reboot can clear temporary glitches and get the dance back on track. Think of it as hitting the reset button on a video game.
- Logbook Wisdom: The drive’s internal data logs hold valuable clues. Examining error messages, timestamps, and operating parameters can shed light on the sequence of events leading to the F9001 incident. Think of it as reviewing security footage to identify the suspicious character.
- Specialized Support: For persistent issues, consulting Rexroth’s technical support or a qualified service technician becomes crucial. As Rexroth specialists, we can track down the culprit and may be able to save you from the need to buy a new drive. Our expertise and access to advanced diagnostic tools can pinpoint the exact cause and recommend the most effective solution. Think of it as calling in a detective with a magnifying glass and keen observation skills.
Beyond the Error: Proactive Measures
Preventing F9001 requires vigilance and proactive maintenance:
- Software Updates: Keeping the drive’s software up-to-date ensures bug fixes and compatibility with newer system components. Think of it as patching leaky windows before the storm hits.
- Regular Checkups: Scheduled inspections and preventative maintenance can identify potential hardware issues before they snowball into major malfunction. Think of it as giving your car a tune-up to prevent engine trouble.
- Training and Awareness: Educating operators and technicians about error codes and troubleshooting procedures empowers them to react swiftly and efficiently when F9001 rears its ugly head. Think of it as equipping everyone with a flashlight to navigate the darkness.
The Final Curtain
Rexroth F9001, though daunting, is not an insurmountable obstacle. By understanding its nature, diagnosing its cause, and implementing preventive measures, you can turn this error into a mere blip on the radar of your operation. Remember, knowledge is your shield, and vigilance is your sword in the battle against unexpected hiccups. So, keep calm, maintain focus, and remember, even the most intricate machinery benefits from a touch of human understanding and care.
Contact us for the fastest solution to Rexroth industrial motion control problems.