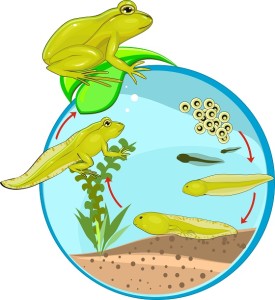
The guys who can repair machinery and troubleshoot mechanical communication problems, see where new solutions need to be brought in and where traditional tactics will still work just fine, and design and configure a workplace in their heads — those guys are, on average, 56 years old. That means that a lot of these invaluable workers have already retired, and more will soon follow.
This is as it should be. You don’t want guys on the factory floor at 92 when they should be out playing golf. The problem is, the retirement part of the industrial lifecycle is still in place, but the other parts aren’t.
Just as a frog goes from an egg to a tadpole, to a mature frog, factory workers used to go from students to apprentices to mature factory workers before they retired.
During the offshoring boom, however, factory workers lost their jobs and factory jobs became less desirable in the minds of students. Shop classes closed down and apprenticeship programs folded. Now there are few students who are prepared — in knowledge or in attitude — to enter industrial jobs.
But some companies are replacing the missing link in the life cycle by offering apprenticeship programs. Rexroth, with roots in Germany where apprenticeships have been holding strong since the Middle Ages, is a leader in this area.
Other companies are following, though. Steel worker apprenticeship programs are springing up in the steel belt, where they show videos of modern steel mills to change the mental image of the grandchildren of steel workers.
Rexroth offers apprenticeships in mechatronics and mchining in South Carolina, where they start their outreach in elementary schools, before the allure of machines gets tarnished by misconceptions about modern factories.
Apprenticeships are the best shot at ending the skills gap and avoiding a shortage of industrial workers in the future. In the meantime, we have the expertise you need to keep your Rexroth electric motion control running.