Sending Rexroth Indramat motors to third party repair shops is kind of like playing Russian Roulette with a fully loaded gun. The only question is how bad is it going to be? The 3rd party shops cannot buy new parts, they do not have access to drawings or technical specifications and in most cases they do not have people who are used to working on high precision servo motors. In some cases, it doesn’t even appear that they have metric tools on site (I would hate to think they are just using vice grips because they figure vice grips will work on everything).
New motor or factory repair?
Our first contestant is a company that had a large drive motor go bad. They they shipped it to a 3rd party house for repair. The motor came back and wouldn’t fire up, because the workmen had used the wrong thermistor values (although they did actually use a thermistor of some value, so it could be worse… as you’ll see later in this post).
When the company called us, they had already been down for an extended period of time for the first repair, and were asking for a new motor. We always enjoy selling new motors of this configuration, although the $98,101.56 cost caused a bit of a silence on the other end of the phone. Once we established the line had not gone dead and no ambulance was required, the 16-20 week lead time was merely the icing on the cake. We then offered factory repair, which is, of course, where they should have been in the first place. With an expedite in place, they trucked the motor up to the repair lab.
On arrival at the repair lab, the first problem was pretty obvious.
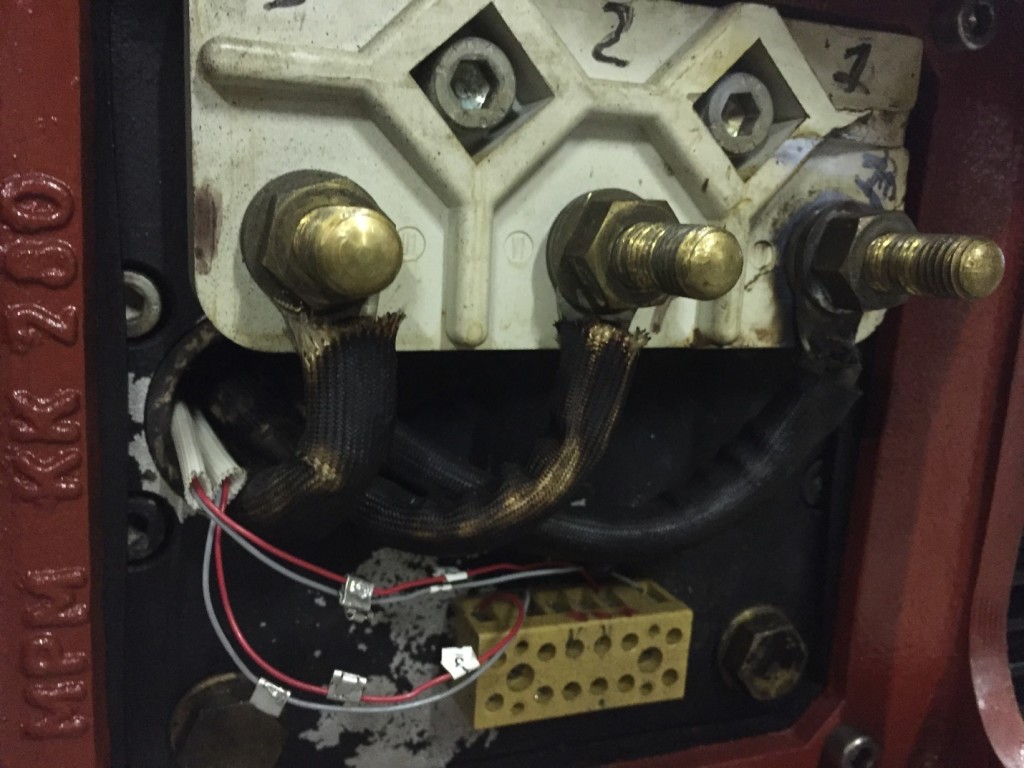
Note the burned power block with the 3rd party thermistor leads (of the wrong value). The leads are not from Rexroth, because 3rd party repair shops can’t buy new parts from Rexroth. They have to just use what they have lying around on the floor, we suppose.
The other problems here were a bit more subtle, but even more troubling. Note the large groove worn into the inside of the seal plate.
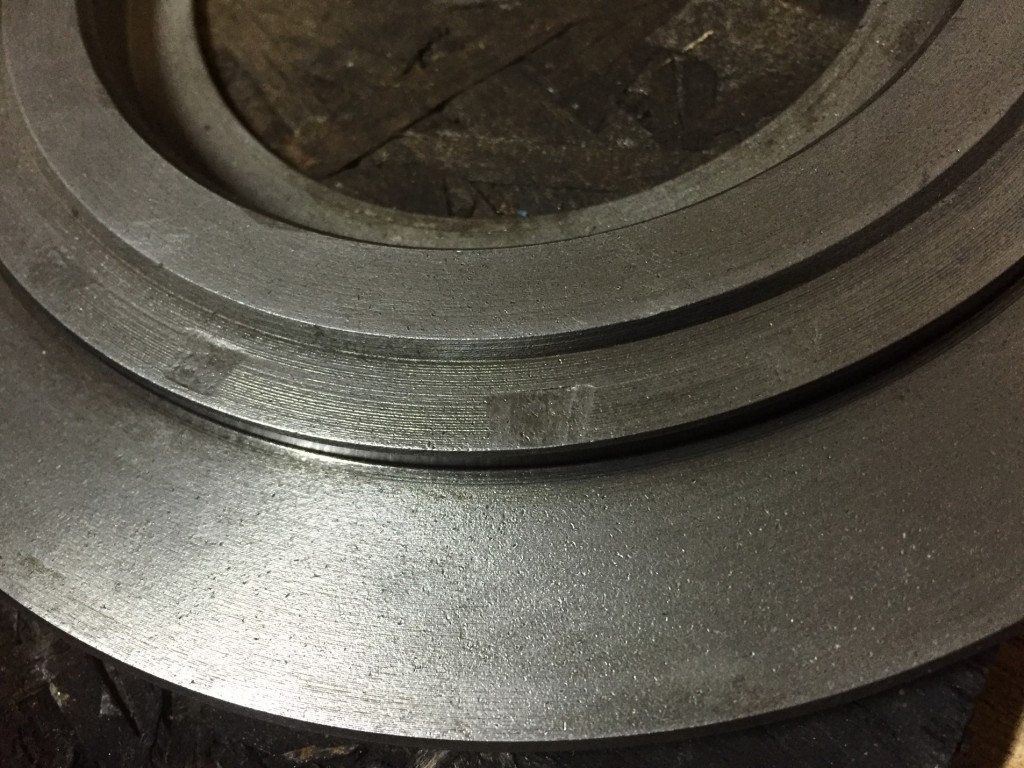
Finally (almost literally) note the stator insert that is slightly protruding.
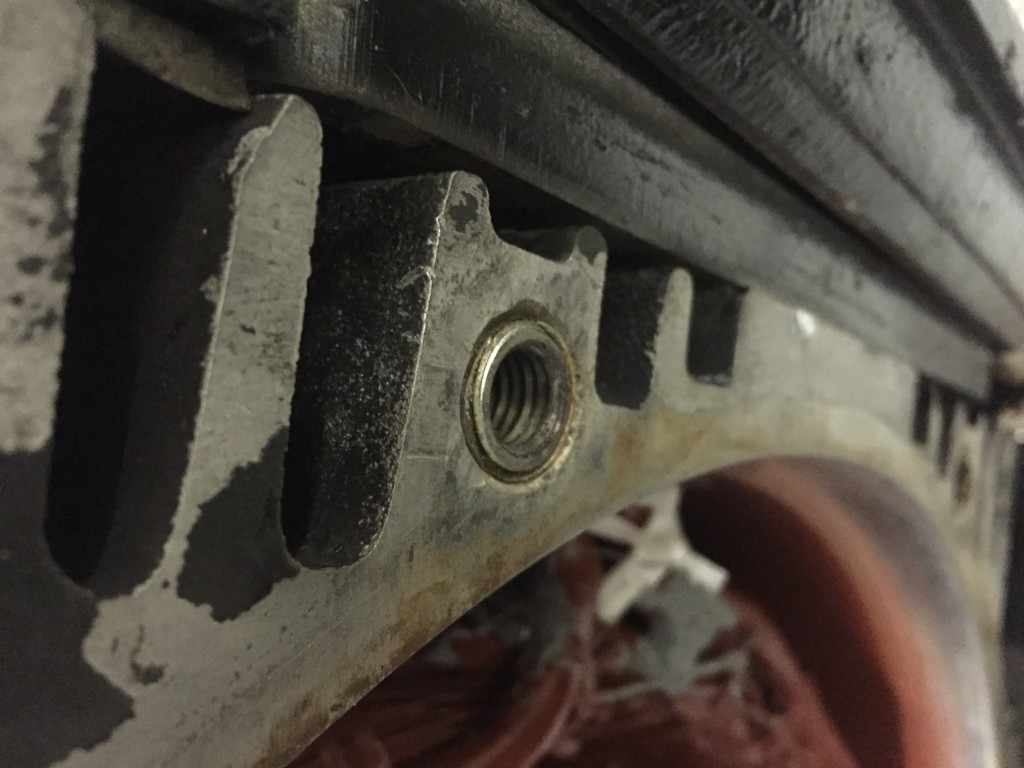
This prevented the end flange from going on straight and caused a concentric runout of .0015”, a value which would not provide for much of a life of the motor if it even would have started. The final shipping value was .0001”, a value that will last for a long service life.
Consequences of trying third party repair
So, the company lost three weeks, they paid an expediting fee that wouldn’t have been necessary had the unit been repaired properly in the first place, and they avoided the bullet of a short lived motor with an expensive breakup and possible collateral damage. The only good thing was that the bad thermistor that the third party shop put in the motor actually saved them further damage by preventing the motor from running.
It would have been so much better had they come to us first. We specialize in Rexroth electric industrial drive and control. We offer factory repair and reman, and we have the largest assortment of emergency replacement parts in the nation.