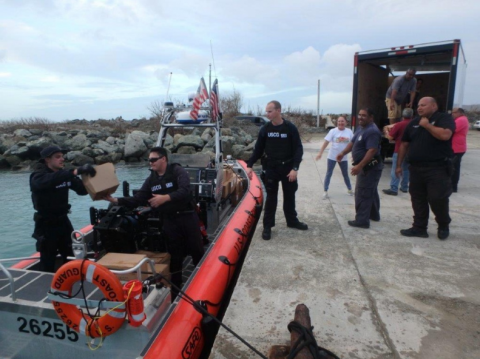
This year’s hurricane season has been one of the worst in history. Hurricane Harvey drenched the gulf coast, causing billions of dollars worth of damage in Texas. Hurricane Irma hit Florida, destroying property and causing widespread evacuations. Then Hurricane Maria moved in, creating catastrophic damage in Puerto Rico, where Hurricane Irma had already knocked out the electrical system.
Texas and Florida saw damage, but Puerto Rico was destroyed. Why? The electric, water, and sewer systems were in bad repair. Trees and debris hadn’t been kept trimmed, so there were lots of things ready to fall on power lines and clog drains. Roads and bridges had been ignored, and quickly became impassible. The air traffic control system was damaged beyond repair.
Water and medical supplies were quickly flown in and brought in by ship, but there were not enough drivers to take the supplies to the people who needed them, even when there were roads that could get them to their destinations. The Governor of Puerto Rico worked closely with the White House to get federal funds in place as fast as possible, but the federal funds paid for just 75% of the cost of the emergency response — without the 25% matching funds, Puerto Rico got nothing. It took more than a week to get a waiver of that rule so Puerto Rico could begin to benefit from the federal funds.
Puerto Rico was not prepared for a couple of major hurricanes.
Your facility may not be in a hurricane-prone area. But the lessons of this year’s hurricane season still apply.
Keep maintenance in mind.
Whether you rely on a routine maintenance schedule or on Industry 4.0 sensors, you can’t ignore maintenance. Clean dust and debris from the area around your servo motors, drives, and controls. Dirt is the enemy of productivity for your motion control system. Debris is also a factor in plenty of industrial fires.
Make sure your cables are in good condition, and keep spare batteries and spare cables on hand.
Error codes give you warning of maintenance issues before the machinery quits working. Get support as soon as you know you need it, not after your machinery has been limping along for a while.
Fresh batteries won’t solve your problems if your facility is hit by a hurricane, but well-maintained machinery is always easier to get back in motion after an emergency than poorly-maintained machinery.
Choose the right service partner.
If disaster strikes, you’re going to need help. For an industrial situation, every minute counts. If you have to bring in a restoration crew, you need to be able to repair or replace your Rexroth units as quickly as you can.
In the midst of a crisis, you don’t want to have to call around in hopes of finding a local repair shop that might be able to cobble something together. You certainly don’t want to have to rely on eBay for replacement units. Third party repair shops don’t have access to original Rexroth parts. The only like-new option for repair of Rexroth electric drive and control systems is factory repair. Going with a cheaper option is likely to leave you with days or weeks of downtime — and maybe calling around again a week later.
Be ready to call us.
When you call us, we provide fast, expert phone support. We have been specializing in Rexroth electric industrial motion control for decades, and we’ve seen it all. Once we’ve established what you need, we get the part to you fast — we have the largest stock of emergency replacement units in the nation, and charter plane service to get what you need to your doorstep. You don’t lose time while your units are expertly repaired or remanufactured at the factory. You get the advantages of new original parts, not something pretty close that happened to be on someone’s shelf, or used parts with no warranty.
Put our number into your phone now. (479) 422-0390 will reach us 24/7.