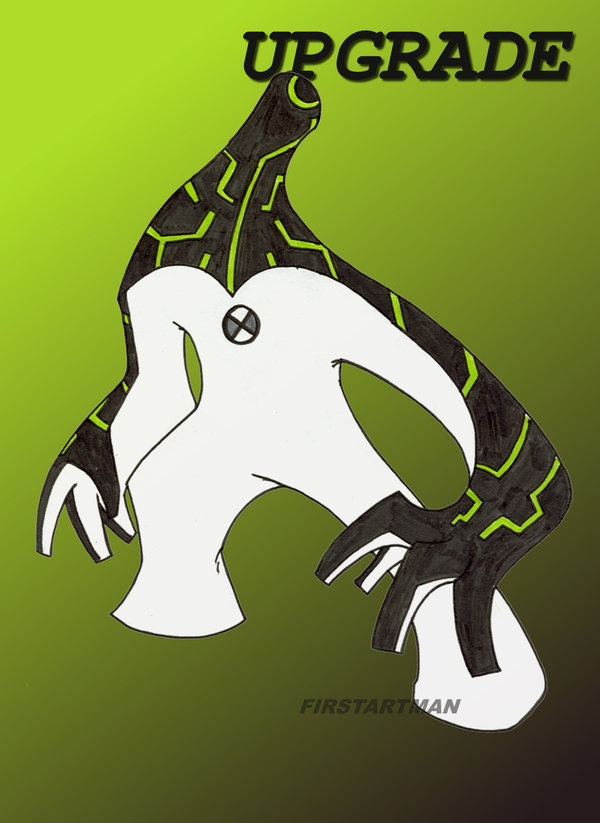
After having been in this business for longer than I care to think about, I find that upgrading is probably the most misunderstood and poorly approached action that people take with their machinery. People who will spend months analyzing the purchase of new equipment will launch into the upgrade of an existing piece of equipment at the drop of a hat.
There are outside drivers of this as well. Sales people, by their nature, want to sell things. Misdiagnosed problems with equipment can make it seem as if an upgrade is the easiest way to get a problem off your back. Inaccurate information (see sales people) can cause premature upgrades when continued support seems in doubt.
Besides, some people always want to have the latest stuff. There are people in this business who don’t want last week’s controls– they want this week’s controls. They are like the guy who has to have the latest phone, ipad or whatever, because it’s the latest, not because he needs it. I would hate to be the accountant who has to try to show a ROI for these types.
There are two basic times that you need to upgrade.
If the control is no longer supportable, you have to upgrade.
This does NOT mean “no longer available new.” Many companies service components for decades after they stop selling them new. Nor does it mean that the controls run under DOS or Win3.11 and Microsoft doesn’t support those any more. Sure, they are unsupported operating systems now, but you are not going to be trying to run Office 2019 or surf the web with them. On the way out the door, the Field Service Engineer grabs his normal computer plus any earlier computer that he needs for the job. We keep several Thinkpad T20 units with DOS loaded for work on a variety of different early controls.
What this does mean is “OEM no longer repairs units.” While there are a number of third party shops that “repair” drives and motors, if the OEM is no longer supporting a piece of equipment, where are the third party shops going to get components from? Of course, that question is also valid for equipment that is still supported, but that is for a different column.
If an upgrade will get you something you need, you should upgrade.
If the current controls can’t handle the speed, accuracy, or new material you need in order to accomplish your goals, it’s time to think about an upgrade. New controls can be justified because they provide cost savings. We had a client who was throwing away 1/16” of an inch of plastic on every package he ran. Setting up the controls differently and upgrading one component allowed a six figure savings per year. We have seen other clients who needed more torque because of bigger raw material. When things change in the rest of the plant and your controls can’t keep up, an upgrade is the way to go.
There’s one more reason we hear a lot about: the upgrade for “Cost Savings” on hardware. This is the one I hear the most about that often makes the least sense. Client has a 1980 machine, and a drive fails. Repair of the drive is quite expensive, much more than the cost of a new drive, so the obvious answer is to upgrade the machine to new drives. Except… there are 3 drives on the machine, and the new drives will not run with the older motors, so now you have 3 new drives along with 3 new motors, and the drives don’t wire up the same so now you are replacing the entire control system with six weeks of downtime on a 30 year old machine you were going to junk next year anyway… That drive repair looking cheaper now?
So you do upgrades when
- You can no longer get repairs done on the equipment, and are running out of spares.
- When it will provide a quantifiable cost justification on the basis of speed, accuracy or capability.
You wait as long as you can for upgrades, because upgrading next year may mean you get a newer control than is available this year, meaning that the lifespan of the control may be several years longer.
For upgrades or for repair, contact us. We specialize in Rexroth electric industrial motion control.
[…] that means that you’ll be repairing or replacing your Indramat units instead of upgrading, give us a call at (479) 274-8422. We have new and factory refurbished units for emergency […]
[…] Then, shaking their heads sadly, the salespeople sell them a whole new system. […]